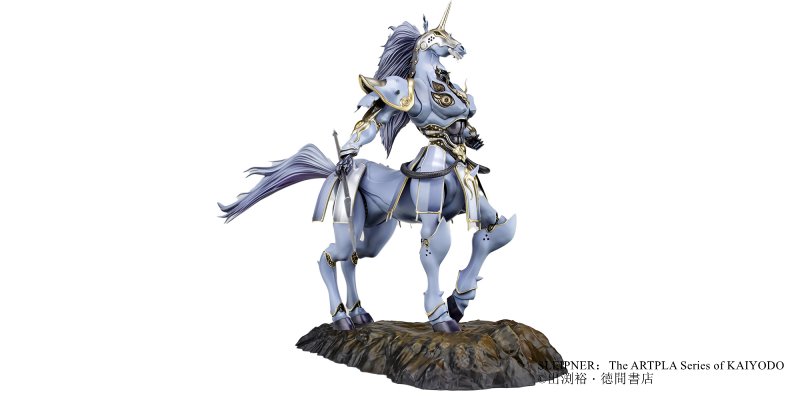
How are action figures produced
The production process of figurines typically includes the following main steps:
1. Design and Prototype Production:
Design: The production of figurines begins with the design phase, which involves determining the appearance, pose, and details of the figurine. The design can be done by professional figurine designers or based on existing artwork with modifications and optimizations. Prototype Production: Based on the design drawings or digital models, a prototype of the figurine is created. Various materials and techniques can be used for prototype production, such as hand carving, digital sculpting, and 3D printing. The purpose of prototype production is to validate the feasibility and effectiveness of the design and to facilitate further processing and improvements.
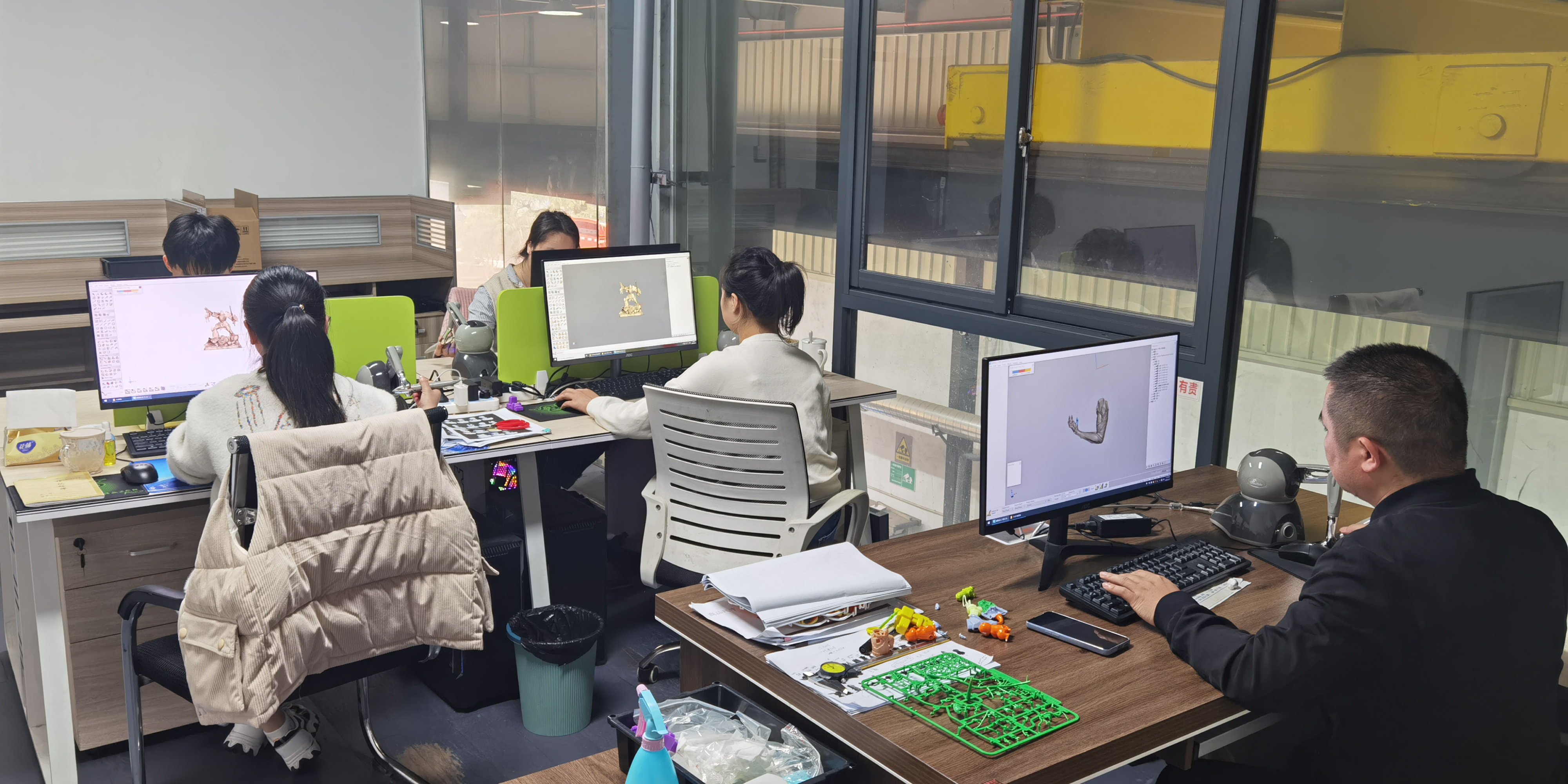
2. Disassembling:
After the prototype design is completed, manufacturers usually determine the number of molds required and perform disassembling of the figurine. Various methods can be used for this process, including 3D scanning and other replication techniques. Here are some common disassembling methods: 3D Scanning: The figurine is scanned using a 3D scanner to obtain a digital model. Scanning allows capturing the geometric shape and detailed information of the figurine, generating a complete digital model. The manufacturer can then use 3D modeling software to disassemble the digital model into multiple parts for mold making. Another method involves coating the figurine with mold material, such as silicone, and creating replicas to perform the disassembling.
3. Mold Making:
Mold Design: The number of molds is determined based on the disassembling process, and different materials are used for mold making depending on the materials of the figurine, such as steel molds, aluminum alloy molds, and silicone molds.
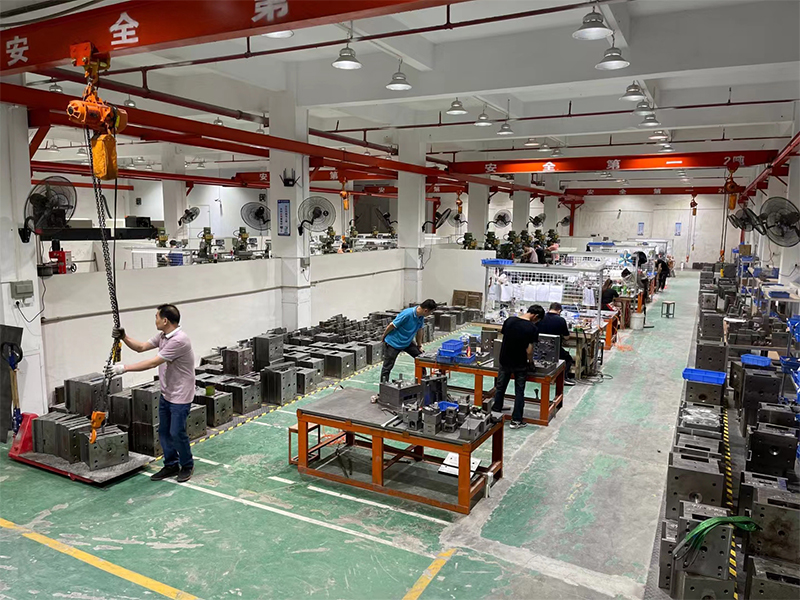
4. Trial Molding and Mold Adjustments:
Trial Molding: Trial molding is a crucial step in the production process of figurines. After the mold is completed, manufacturers install it onto an injection molding machine and inject molten plastic material to create a prototype of the figurine. The purpose of trial molding is to test the performance of the mold and the injection molding process for the figurine. During the trial molding process, manufacturers adjust parameters of the injection molding machine, such as temperature, pressure, and injection speed, according to the design requirements and expected results. This ensures a smooth injection process and the production of figurines that meet the required specifications. If any issues are identified during the trial molding, manufacturers may need to conduct multiple trials, make parameter adjustments, and modify the mold until the desired injection results are achieved.
Mold Adjustments: Mold adjustments are carried out during or after the trial molding process. Manufacturers may encounter issues or identify areas for improvement during the trial molding. These issues could include inaccurate dimensions, unsatisfactory surface quality, or poor fit between parts of the figurine. To address these issues, mold adjustments are performed. The process involves repairing specific areas of the mold, adjusting mold dimensions, and refining the mold surface. Through mold adjustments, manufacturers can improve the mold's performance and ensure that the quality of the figurines meets the required standards. Mold adjustments are typically carried out by experienced technicians who take appropriate measures to adjust and improve the mold based on the trial molding results and the requirements of the figurines.
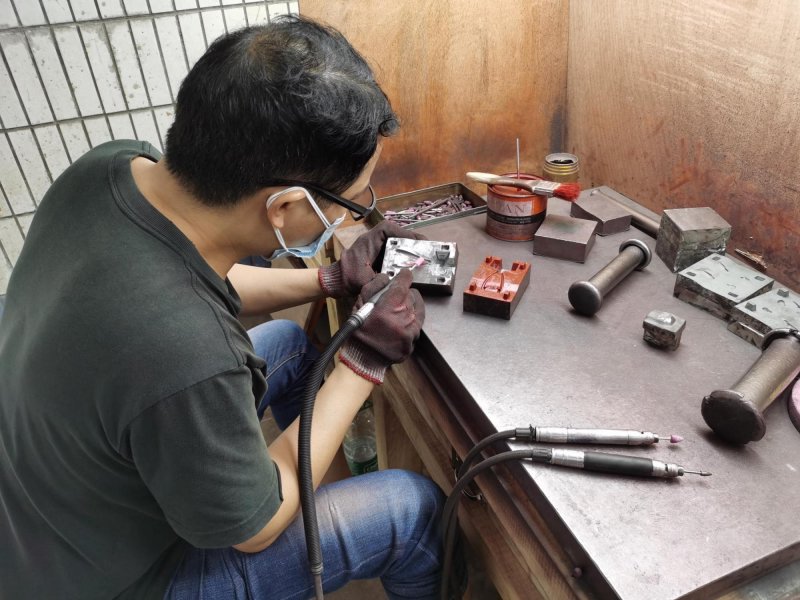
The goal of mold adjustments is to enable the mold to produce high-quality figurines and ensure that every detail of the figurines aligns with the design requirements. ITTAK has extensive experience in figurine mold manufacturing and aims to minimize the number of mold adjustments required, achieving MP (Mass Production) level in the shortest possible time.
5.Injection and Assembly:
Injection: Liquid plastic is injected into the mold using the mold, and after heating and cooling, the plastic solidifies into the shape of the figurine. Injection typically involves the use of plastic materials such as polypropylene (PP) or polyvinyl chloride (PVC).Separation and Cleaning: The injection-molded figurines are removed from the mold and undergo cleaning and trimming to remove any potential defects and excess material.
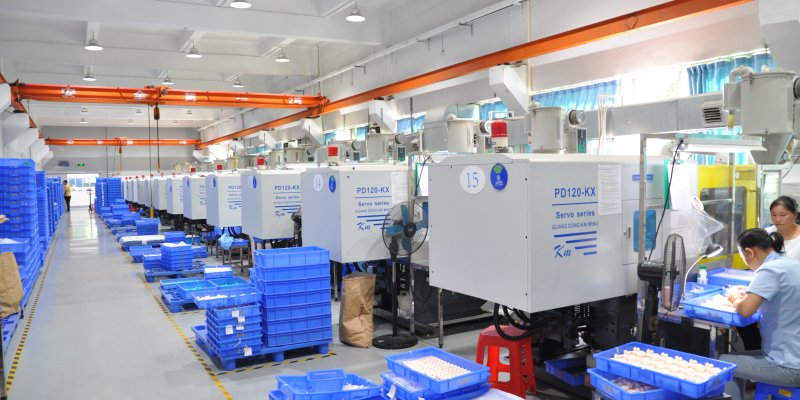
Assembly and Painting: The various components of the figurine are assembled, including connecting joints and adding accessories. Depending on the design requirements, the figurine may undergo coloring and painting to enhance details and texture.
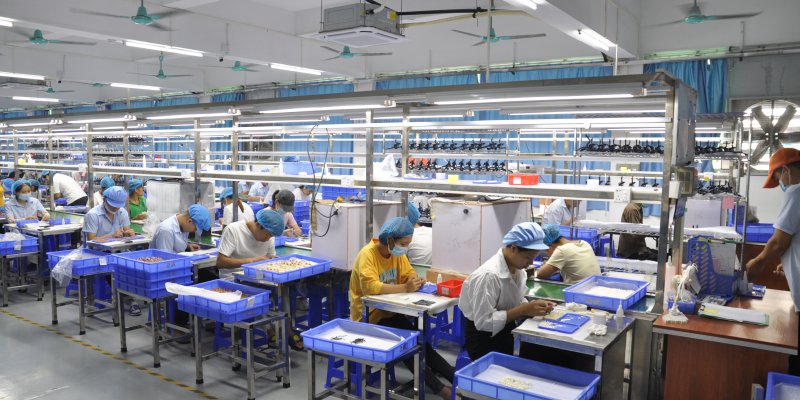
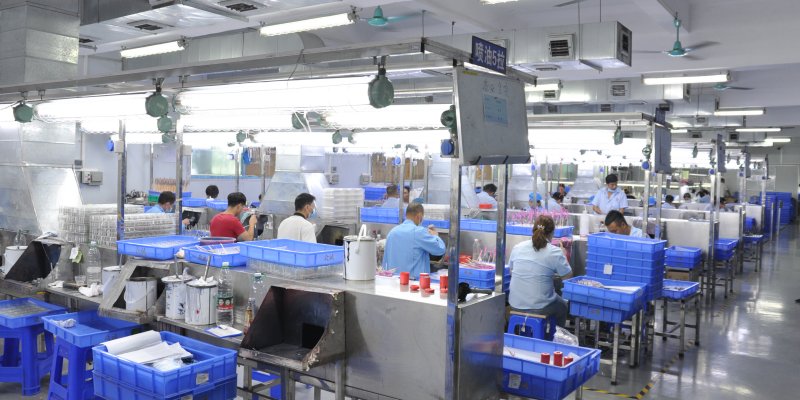